Incident Overview
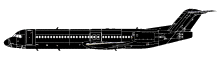
Description
TAM flight 402, a Fokker 100, crashed following thrust reverser deployment after takeoff from S?o Paulo-Congonhas Airport, SP, Brazil, killing all 95 occupants and 4 persons on the ground. Flight 402 was a regular domestic flight between S?o Paulo (CGH) and Rio de Janeiro (SDU), Brazil. At 08:25 the flight received clearance for takeoff from runway 17R. Wind was given as 060 degrees. At 08:26:00 the throttles were advanced for takeoff power. Ten seconds later a double beep was heard. The captain said “O auto-throttle t fora” and the copilot adjusted the throttles manually and informed the captain: “thrust check”. With this information he confirmed that the takeoff power had been adjusted and verified. At 08:26:19 the airplane accelerated through 80 kts. At 08:26:32 the copilot indicated “V one”. Two seconds later the airplane rotated at a speed of 131 kts. The speed increased to 136 kts and the airplane was climbing at an angle of 10 degrees. At that same moment a shock was felt and the EPR of engine no. 2 dropped from 1.69 to 1.34, indicating the loss of power. In fact, the no. 2 engine thrust reverser had deployed. An eye witness confirmed to have seen at least two complete cycles of opening and closing of the no. 2 thrust reverser buckets during the flight. The loss of power on the right side caused the plane to roll to the right. The captain applied left rudder and left aileron to counteract the movement of the plane. The copilot advanced both thrust levers, but they retarded again almost immediately, causing the power of the no. 1 engine to drop to 1.328 EPR and engine no. 2 to 1,133 EPR. Both crew members were preoccupied by the movement of the throttles and did not know that the thrust reverser on the no. 2 engine had deployed. The throttles were forced forward again. At 08:26:44 the captain ordered the autothrottle to be disengaged. One second later the no. 2 thrust lever retarded again and remained at idle for two seconds. The airspeed fell to 126 kts. At 08:26:48 the copilot announced that he had disengaged the autothrottles. He then jammed the no. 2 thrust lever fully forward again. Both engines now reached 1,724 EPR. With the thrust reverser deployed, the airspeed declined at 2 kts per second. At 08:26:55 the stick shaker activated, warning of an impending stall. The airplane rolled to a 39 degree bank angle and the GPWS activated: “Don’t sink!”. Seven seconds later the airplane impacted a building and crashed into a heavily populated neighborhood. a. Contributing Factors Psychological Aspect – Contributed a) organizational aspect The lack of information, instructions in writing and practice, contributed to the non-recognition of the abnormality during its unfolding. b) Individual aspect The unusual occurrence of the quick reduction of the lever, on a particularly difficult phase of the operation (transition from take-off run to flight); the nonoccurrence of failure discriminating (sound and visual) warnings, and the lack of cognizance and specific training for such abnormality bring on surprise and distraction of the crew members’ attention. – The release of the restriction of the lever of engine 2 at the idle detent without the occurrence of the abnormality warnings strengthened the tendency (in at least one of the crew members) to try to recover the power on the engine. – The lack of warnings and the difficulties that are characteristic of such abnormality have diverted the crew members’ concentration from the procedures provided for, to concentrate it on the solution of the abnormality, initially imagined as being an auto-throttle failure, and later the recovery of thrust – The occurrence of auto-throttle failure warnings (before the 80 Kt) and the lack of specific reverse opening warnings (Master Caution and RSVS UNLK) have strengthened, in the crew members, the belief that they were experiencing an autothrottle failure (illusion). b. Material Factor (1). Desing Deficiency – Contributed The reverser fault tree chart made recently by the manufacturer considering the Post-Mod version, even not taking into account a dormant fail, has indicated that the probability of an inadvertent opening of the reversers is of the order of 10″6. The Post-Mod version does not meet the airworthiness requirements of FAR/RBHA 25.1309. On two phases of the complete reversers cycle, at the beginning of the opening and at the end of the shell closing, it is possible to apply power higher than IDLE with the shells partially open, which does not meet RBHA/FAR 25.933. The reverser unlocked indication system is inhibited at speeds higher than 80 Kt and up to the height of 1000 feet, exactly at an instant when the pilots would need such information most. The SECONDARY LOCK ACTUATORS (S/N 874 and S/N 870) that equipped the aircraft that suffered the accident, on the operational tests proposed and carried out, presented a performance much below the minimum acceptable to assure the safety and reliability of the system. The applicable FAR 25.993(a)(3) requirements determine that each [reverse] system is to be provided with means to prevent the engine from producing power higher than idle power upon a failure on the reverse system [not stipulating the type of failure]. Such requirement has not been complied with, both in relation to the control system, which permitted the shells to open in flight, and in relation to protection, which became non-existent when the separation of the FEEDBACK CABLE occurred due to the unpredicted pilot’s action on the lever, with the intention of recovering the power of the affected engine. The TURNBUCKLE is installed on the side to which the connection moves when the reverser is commanded to open, i.e., the same side towards which the connection moves when the situation occurs in which the lever is forcibly held forward while the reverser is opening (deploying). The THRUST SELECTOR VALVE may be moved with less than 2% of the normal functioning pressure, when the selector valve is de-energized, which was the condition at the time of the accident. The inductive loads as those of SEC. LCK. ACTUATOR are detrimental to the contacts that command them, particularly on de-energization, in case there is no protection diode, which is apparently the case of SEC. LCK. ACTUATOR. The THRUST REVERSER ACTUATOR, in the Post-Mod configuration, incorporated to the assembly line by the manufacturer, remains de-energized during the periods in which there is no commanding by the pilot, and this way it stays in an unstable and dangerous situation. Design faults,
Source of Information
http://g1.globo.com/Noticias/0,,IIF1041-5605,00.htmlhttp://g1.globo.com/Noticias/0,,IIF1041-5605,00.htmlPrimary Cause
UnknownUnknownShare on: