Incident Overview
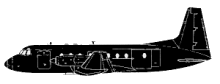
Description
The HS-748 was cleared for a runway 23 takeoff at 23:29. The first officer was the handling pilot and the takeoff was to be made with full dry power; the water methanol system was selected to standby. At an airspeed of 111 kt the Commander called ‘vee one, rotate’, the first officer moved the control column rearwards and the aircraft became airborne. Less than five seconds after the ‘rotate’ call, at an airspeed of 115 kt and a height of between 30 feet and 100 feet agl, the no. 2 engine suffered a catastrophic failure resulting in a sudden loss of power and an immediate substantial nacelle fire. The aircraft yawed 11deg to the right of the runway heading. The Commander took over control and the crew were told by the senior cabin attendant that the right engine was on fire. Engine power was reduced and the aircraft yawed 14.5ø to the left of runway heading. Four seconds later, the sound of the engine fire warning bell was recorded. The aircraft was in the air for a total period of 27 seconds before it touched down. The aircraft ran off the end of the runway at 62 kt., crossed the perimeter track and came to rest with the collapse of the nose landing gear. CAUSAL FACTORS: “1. Significant reduction in the fatigue strength of the HP turbine disc due to surface corrosion. 2. Inadequate control of the fit between engine turbine assembly seal members, possibly influenced by inadequate turbine clamping bolt fit, causing sufficient reduction in the natural frequency of an HP turbine disc vibratory mode to allow its excitation within the normal operating speed range and consequent excessive stressing of the disc. 3. Fuel leakage from the engine bay fuel system, resulting in a major nacelle fire. 4. Failure to identify the turbine assembly seal member fit and HP turbine disc corrosion as possible contributors to disc fatigue damage after previous similar failures.”
Primary Cause
Significant reduction in the fatigue strength of the HP turbine disc due to surface corrosion, coupled with inadequate control of the fit between engine turbine assembly seal members, potentially influenced by inadequate turbine clamping bolt fit, causing sufficient reduction in the natural frequency of an HP turbine disc vibratory mode to allow its excitation within the normal operating speed range and consequent excessive stressing of the disc.Significant reduction in the fatigue strength of the HP turbine disc due to surface corrosion, coupled with inadequate control of the fit between engine turbine assembly seal members, potentially influenced by inadequate turbine clamping bolt fit, causing sufficient reduction in the natural frequency of an HP turbine disc vibratory mode to allow its excitation within the normal operating speed range and consequent excessive stressing of the disc.Share on: