Incident Overview
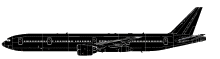
Description
Singapore Airlines flight SQ368 departed Changi Airport at 02:05 local time for a flight to Milan-Malpensa Airport, Italy. About 30 minutes into the flight, when the aircraft had climbed to 30,000 feet, the flight crew noticed that the oil quantity parameter in the Engine Indicating and Crew Alerting System (EICAS) showed 17 units for the left engine but only 1 unit for the right engine. The flight crew also noticed from the EICAS display that the right engine oil pressure was fluctuating between 65 and 70 psi while the oil temperature for the right engine was 10øC higher than the left engine. However, both the oil pressure and temperature parameters were within the normal operating range. The flight crew looked through their available manuals but was unable to find an appropriate procedure that addressed the low engine oil quantity situation. At 03:04 hours, the Pilot-in-command (PIC) contacted their company’s engineering control centre for assistance. The engineer informed the PIC that since the oil pressure was within the normal operating range, there could be a faulty oil quantity indication. The engineer advised the PIC to continue with the flight but monitor the right engine oil parameters. The engineer told the PIC that he would also contact the company’s technical services personnel for advice. After being briefed by the engineer on the situation, the technical services personnel believed that it was a faulty oil quantity indication. As the aircraft had just departed and was not far from Singapore, the technical services personnel recommended that the aircraft return to Singapore. According to the flight crew, as they were passing waypoint VPG at approximately 03:20 hrs, the First Officer performed a routine fuel quantity check. After comparing the TOTALIZER fuel quantity with the planned fuel remaining quantity, it was determined that the fuel consumption was better than expected as the fuel on board was 600 kg more than the expected value. At 03:28 hrs, the engineer sent a message via the Aircraft Communication and Reporting System (ACARS) to the flight crew informing them about the recommendation by the technical services personnel for the aircraft to return to Singapore and requesting them to contact the engineering control centre. The PIC contacted the engineering control centre and a conference call among the PIC, the engineering control centre and the technical services personnel was held, which lasted for about 20 minutes. The PIC informed the rest that the flight crew had been monitoring the right engine oil parameters for 50 minutes and other than the indicated low oil quantity, the parameters appeared normal. It was jointly assessed that the flight could continue to Milan with the proviso that the flight crew monitor the right engine oil parameters and contact the engineering control centre for assistance if needed. Shortly after the conference call ended, the flight crew felt an unusual vibration in the control column and cockpit floor. The flight crew tried to diagnose the problem by changing the engine power settings and found that the vibration disappeared when the power of the right engine was reduced. At about the same time, the flight crew caught a momentary wisp of burnt smell in the cockpit but the smell disappeared quickly. At 04:04 hrs, the PIC informed the engineering control centre about the vibrations which the flight crew experienced whenever the right engine was operated at higher power settings. In the ensuing conference call among the PIC, the engineering control centre and the technical services personnel, it was assessed that there was no need to shut down the right engine and decided that the aircraft would return to Singapore with the right engine operating at idle power. In the midst of the conference call, the In-flight supervisor (IFS) informed the flight crew that there was a burnt smell detected in the cabin. In response, the flight crew turned off the right engine bleed system. According to the cabin crew, the smell was particularly strong in the forward part of the aircraft. The cabin crew distributed wet towels for the passengers to hold over their nose and breathe through it. After the conference call ended, the flight crew reduced the right engine to idle power and proceeded to turn the aircraft around to return to Singapore. For the return journey to Singapore, the flight crew adopted the procedure for single engine operation, including a descent to 17,000 feet before reducing the right engine to idle power. When the IFS informed the flight crew that the burnt smell in the cabin was still present, the right air conditioning pack and recirculating fans were switched off. Shortly after, the smell in the cabin subsided. At 05:21 hrs, the flight crew received a FUEL DISAGREE message on the EICAS. The flight crew performed the FUEL DISAGREE checklist. The FUEL DISAGREE checklist suggested four scenarios in which a fuel leak should be suspected and when the flight crew should perform the FUEL LEAK checklist. One such scenario is when the TOTALIZER fuel quantity is less than the CALCULATED5 fuel quantity. The flight crew observed from the display of the flight management system that TOTALIZER fuel quantity was about 79 tonnes and the CALCULATED fuel quantity was about 83 tonnes. However, the flight crew did not perform the FUEL LEAK checklist. According to the flight crew, they believed the CALCULATED fuel quantity was no longer accurate because input changes had been made to the flight management system after the right engine was set to idle power and they were no longer on the planned flight route. Thus, the flight crew performed their own fuel calculation by subtracting the amount of fuel consumed from the total amount of fuel at the start of the flight. The fuel consumed was calculated to be about 79 tonnes. As this tallied well with the TOTALIZER fuel quantity figure, the flight crew concluded that the FUEL DISAGREE message was a spurious one and that there was no need to proceed with the FUEL LEAK checklist. Several times on the return journey and as the aircraft approached Singapore, the flight crew was queried by the Air Traffic Control (ATC) if they needed any assistance. The flight crew replied that, other than the need to fly at the lower altitude of 17,000 feet, no assistance was needed as all other operations were normal. Prior to landing, the flight crew jettisoned about 41,500 kg of fuel to bring the aircraft to below its maximum landing weight. At 06:49 hrs, the aircraft landed on runway 20C. About 20 seconds after the thrust reversers on both engines were deployed, the occupants in the cabin heard two loud bangs, accompanied by two flashes, originating from the right engine area. At the same time, the flight crew heard a soft thud. The Airport Rescue and Firefighting Service (ARFF) personnel who were monitoring the aircraft’s arrival informed the Control Tower on seeing the fire at the right engine. The Control Tower informed the flight crew of the fire and instructed the aircraft to stop at the intersection between the runway and rapid exit taxiway E7. The flight crew did not receive any fire warning in the cockpit. The first foam tender arrived on scene after 57 seconds and started discharging foam at the right engine. The fire was eventually brought under control after about two minutes. Disembarkation commenced at 07:10 hrs via a mobile stairs positioned at the front left door of the aircraft. All occupants, including the flight crew, vacated the aircraft by 07:31 hrs. CONCLUSION 1 The fuel leak in the occurrence flight was a result of a cracked tube within the MFOHE of the right engine. Fuel leaked into various areas of the engine through the core of the engine and the fan duct. 2 When the thrust reverser was deployed during landing, the conditions at the area aft of the turkey feather seal of the core exhaust nozzle resulted in hot surface ignition of the fuel that had leaked from the MFOHE into the various areas of the right engine. 3 As the fire developed, it propagated towards the forward section of the engine and entered the core of the engine through the fan booster inlet. 4 The methods that were used to detect fuel leakage into the engine system by the operator and engine manufacturer were not able to detect the fuel leak that resulted from the cracked tube within the MFOHE when it occurred in that event flight. 5 The engine manufacturer issued SB 79-0034 to address the issue of possible fuel leak in the MFOHE. The deadline for incorporating the SB was determined using the CAAM. The actions called for by the SB was not performed on the occurrence engine as the SB was issued after the engines last maintenance. 6 In the course of the investigation, the engine and MFOHE manufacturers have identified that diffusion bonding can potentially cause any tube in the MFOHE to crack. 7 The flight crew did not execute the steps in the FUEL DISAGREE checklist correctly. 8 The flight crew depended on the fire commander as their sole information source when deciding whether an evacuation was needed. Several other resources which could have aided them in making their decision were not utilised.
Primary Cause
Cracked MFOHE tube within the right engine.Cracked MFOHE tube within the right engine.Share on: