Incident Overview
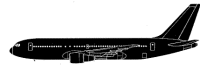
Description
While climbing through FL110, the crew heard a loud ‘bang’ and felt the aircraft move to the right, followed by a progressive yaw to the left. After checking instrumentation, the failure of the left (number-one) engine was confirmed and the engine was shut down. An emergency was declared and the aircraft returned to Brisbane. An initial engineering examination of the left engine revealed a large rupture of the outboard core cowl and severe gouging and scoring of the outboard side of the engine strut above the cowl damage. The leading edge flap panel above the strut was extensively damaged over approximately 40cm and the no. 2 canoe fairing behind the engine sustained debris impact and puncture damage. Inspection of the engine core beneath the ruptured cowl revealed that the first-stage high-pressure turbine disk had failed and released a large segment of the disk rim and outer web. The engine casing around the disk had been completely severed and the central shaft fractured between the stage-one and stage-two high-pressure turbine disks. FINDINGS: – The technical investigation of the failed CF6-80A stage-1 high-pressure turbine disk (s/n. MPOP-8478) found that the disk failed as a result of the initiation and growth of fatigue cracking from the rear bottom corner of a turbine blade fir tree slot. – The disk had developed a total of three slot bottom fatigue cracks at the time of ultimate failure. – None of the cracks were attributable to any identified erroneous tool or handling damage to the slot bottoms. – The disk had undergone a repair operation in August-October 1998. The repair was conducted to remove fir tree slot edge nicks and other damage and included blending of the damage followed by shot-peening of the rear slot edges and other areas. – All of the cracked fir tree slots and several other uncracked slots showed surface microstructural flow and damage that was attributable to the shot peening operation following the 1998 repair. – The type of surface damage produced (specifically the formation of stress-raising defects known as peened surface extrusion folds) has been shown to be detrimental to the fatigue life of the affected component. – The disk had operated for 7,838 hours and through 2,793 cycles following return to service after the August 1998 overhaul. – The previous CF6-80C2 stage-1 HPT disk failure (September 2000) occurred 1,675 cycles after a similar blending and shot peening repair of disk slots and rear corners. – The corrective action implemented after the September 2000 disk failure did not encompass the CF6-80A stage-1 HPT disks.
Primary Cause
Fatigue cracking from the rear bottom corner of a turbine blade fir tree slot during the initial operation of the CF6-80A stage-1 high-pressure turbine disk.Fatigue cracking from the rear bottom corner of a turbine blade fir tree slot during the initial operation of the CF6-80A stage-1 high-pressure turbine disk.Share on: