Incident Overview
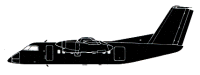
Description
The aircraft was scheduled to complete a flight test following major repairs to the left wing and fuselage. These were carried out in Broome to repair damage resulting from a birdstrike which occurred in May 1996. The crew for the flight comprised two experienced pilots, one of whom was a qualified test pilot, and a flight test engineer. There were no passengers. When the landing gear was selected up, after takeoff, the nose landing gear door unsafe and landing gear handle lights remained on. The gear was selected down and safe indications were obtained. The gear was selected up a second time and it retracted normally. The test flight was continued, with sequences being completed up to the landing gear tests. Landing gear down selection resulted in a safe indication on the main gear (two green lights) and unsafe indications on the nose gear (a red gear light, no amber door light and a light in the gear handle). Actions were completed in accordance with the abnormal and emergency checklist however, the nose gear continued to indicate unsafe. An inspection by ground engineers, during a fly-past, determined that the nose gear was still retracted but the gear doors were partially open. Positive-gravity manoeuvres and a touch-and-go landing failed to shake the nose gear free. The crew decided to land at Broome once all other traffic was clear and emergency services were in place. Advice from the manufacturer’s representative in Broome indicated that the propellers would remain clear of the runway during the landing. A landing was completed with the aircraft sliding to a stop on its main wheels and nose, 460 m after touchdown. It is probable that motivation, pressure and fatigue were the main factors in the decision not to complete the maintenance control manual requirements prior to manufacturing the replacement cover plate. It is likely that the maintenance engineers allowed their desire to get the job done to overcome any caution developed through experience. Limited time availability meant that ordering a replacement part, or ensuring the completion of the required design and approval process, would prevent them meeting the deadline. Fatigue may have reduced the maintenance engineer’s analytical ability and possibly contributed to the flawed decision. The lack of a project manager to supervise and audit the complete engineering process meant there was no safety net to prevent incorrect decisions or practices, emanating from the workface, having a detrimental affect on safety. The lack of a project manager and the limited presence of the technical manager also meant there was no one of authority that the maintenance engineers could readily discuss the problem with before they made their final decision. The fact that the cover plate was not a structural component and was only a protective cover probably misled the maintenance engineers into believing that the manufacture of a similar, but not exact, replacement part would not significantly affect safety. The ultimate safety net, landing gear retraction tests, failed when the cover plate was not fitted prior to the tests. The plate was not fitted because it was not seen as a significant part of the landing gear system and time pressure probably led maintenance personnel to believe that the tests could not wait until assembly was complete.
Source of Information
https://aviation-safety.net/database/record.php?id=19960517-2https://aviation-safety.net/database/record.php?id=19960517-2Primary Cause
Pressure, fatigue, and a lack of oversight due to inadequate management and authority within the maintenance team, leading to a rushed decision-making process and a failure to adhere to established safety protocols.Pressure, fatigue, and a lack of oversight due to inadequate management and authority within the maintenance team, leading to a rushed decision-making process and a failure to adhere to established safety protocols.Share on: