Incident Overview
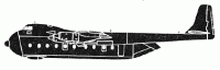
Description
While taxiing after a normal landing, a rumbling noise was heard from the vicinity of the nosegear, the hydraulic low pressure light illuminated and nosegear steering authority was lost. The right hand nosewheel had separated from the aircraft due to fracturing of the axle. As the nosewheel departed it damaged the nosegear uplock assembly with consequent loss of hydraulic system integrity. It then continued under the fuselage causing skin damage. The nosewheel axle was recovered and subjected to metallurgical examination which showed that the fracture was due to fatigue. The fracture resulted from prior long term fatigue cracking which occupied approximately 75 of the cross sectional area of the axle. Stress corrosion cracks were present which were the most likely initiator of the fatigue cracks. A mandatory crack inspection requirement called up for this axle did not cover the specific area in which the stress corrosion was located. Consequently, during the axle refurbishment, the stress corrosion cracks were covered by a layer of electroplated chromium. Significant Factors: 1. The nosewheel axle failed due to fatigue initiated by stress corrosion cracks. 2. The recurrent Non Destructive Inspection for the axles does not address the area where the stress corrosion occured. Consequently, pre- and post- refurbishment inspections did not detect the cracks.
Primary Cause
Stress corrosion cracking initiated by fatigue caused by prior long-term fatigue cracking within the axle.Stress corrosion cracking initiated by fatigue caused by prior long-term fatigue cracking within the axle.Share on: