Incident Overview
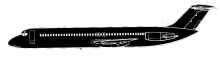
Description
SAS flight SK551 was a scheduled passenger flight between Copenhagen, Denmark and Amsterdam, Netherlands, carrying 102 passengers and a crew of 6. The aircraft took off from runway 22R at Copenhagen Airport at 10:04 hours local time. The co-pilot, who was under route training, performed the takeoff and climb-out. The take-off run was normal. The aircraft started to drift to the right immediately at rotation and lift-off, which was noticed by both pilots and commented by the captain. The co-pilot corrected the yaw by means of left rudder input and subsequent trim, and without problems he engaged the autopilot with the aircraft being trimmed 3 – 4 units left trim input. As the speed increased, the mistrim increased. After disengagement of the autopilot the copilot trimmed up to 9 units left. At that point he informed the captain of the magnitude of the trim. The captain took over, reduced the speed, and started troubleshooting. The troubleshooting consisted in feeling the aircraft’s reaction to manual rudder at different speeds, yaw damper influence, and possible spoiler floating. The malfunction check-list was consulted afterwards. Nothing could be found to explain the rudder mistrim. After discussion between captain and co-pilot, and in agreement with the company maintenance control centre, which was contacted, the captain decided to return to Copenhagen. The rudder control had been returned to powered rudder in order to achieve best effectiveness. The captain has stated that he was concerned about a suspected increase in the minimum control speed. The captain decided to follow parts of the emergency landing check-list by selecting 25 flaps instead of full flaps and not arming the spoilers. He had previously informed the purser and the passengers about the return as being due to a minor technical fault. He saw no reason to declare an emergency, and consequently the cabin was not prepared for one. The approach was performed with some overspeed. According to the captain’s statements, he decided to add about 10 kts to the approach and threshold speed of 139 KIAS in order to be well above the minimum control speed of 135 KIAS. From the flight data recorder the speed at touch down was measured to approximately 160 kts. Rudder trim was 6.5 units left with ailerons trimmed left. The approach and landing was uneventful up to the point when the aircraft began to drift off to the right. The nose wheel touched down approximately 600 metres from the threshold of the runway. When the nose was lowered and the captain had to neutralize rudder in order to line up the nose wheel, the aircraft immediately veered to the right. The captain immediately applied left rudder – which soon became full rudder, full left wheel breaking, and later full left reversing. The aircraft left the runway sideslipping slightly to the right, rolled on the grass along the runway, still sideslipping slightly (around 7ø) , crossed runway 12/30, hit a marker board with the right main gear, and gradually returned to the right side of the runway. At this point the captain reduced left reversing as he felt tendencies to an impending ground loop. The nose gear hit a concrete well cover outside the runway. The final collapse of the nose gear occurred during the last part of the landing sequence, and the aircraft finally came to rest on the runway with the nose off-centered slightly to the left. The aircraft stopped approximately 1500 metres from the threshold. After completion of the “on ground emergency check-list”, neither the emergency power light nor the public address blue light came on when the captain had pressed the light cap. As the captain had trouble in finding the hand set, which had fallen to the floor, he rose to open the cockpit door. He was met by the purser, who then, on order from the captain, ordered emergency evacuation over the megaphone. Four passengers were brought to hospital with injuries incurred during the evacuation. Causal factors: – The cause of the displaced rudder was a cracked rudder torque tube drive crank being displaced 2 splines on the torque tube. This displaced the rudder to the right with neutral pedals and reduced rudder effectiveness to the left considerably, as well as it increased the minimum control speed by an unknown amount. – The crack in the rudder torque tube drive crank had primarily propagated as fatigue and ended up with final fracture of ductile appearance. – The influence of the displaced rudder when centering the rudder pedals on nose wheel contact was unpredictably strong. The insufficient countereffect of the rudder rendered the captain unable to keep the aircraft on the runway.
Primary Cause
Cracked Rudder Torque Tube Drive Crank ? Fatigue and FractureCracked Rudder Torque Tube Drive Crank ? Fatigue and FractureShare on: